Compact Steering System - CSS
Detailed description of the CSS
​
The compact steering system CSS with a monitor and compensation device is composed of three main components:
-
the inner wheel containing the wheel hub, the steering axle, the steering house and the wheel spindle together forming an integral housing
-
the hydraulic or electric actuators ensuring the steering
-
the monitor and compensation device with the Electronic Control Unit (ECU) ensuring a perfectly synchronous steering angle of the wheel hub with and the steer based on information from the angle sensors
​
Click here to look at figures of CSS
The inner wheel contains three main components (figure 1):
-
the wheel hub (1)
-
the steering house (2) and the wheel spindle (4) forming an integral housing for the actuator being a rotary (10) or piston actuator (15)
-
the steering axle (3)
The wheel hub (1) consists of two halves that are connected using bolts (5). The wheel (6) spins around a wheel hub (1) by means of bearings (A). On both sides of the wheel hub (1) side plates (7) are fixed using bolts (8), on which brake callipers can be fitted. The wheel bearings (A) are clamped in the inner wheel (6) together with the spacer (9). The wheel is positioned on the wheel hub (1) using the side plates (7).
The wheel hub (1) encloses the steering house (2) and is linked to the steering axle (3). The wheel hub (1) can rotate around the steering house (2) by means of bearing (B). The steering axle (3) rotates in the steering house (2) by means of bearing (C).
The steering house (2) and the wheel spindle (4) together forming an integral housing for the hydraulic actuator, are situated centrally in the wheel hub (1) when seen in a top view of the wheel (6). The wheel spindle (4) is held from both sides by the suspension arms connected to the frame of the vehicle. The wheel spindle (4) can also be connected to the frame through a single-sided suspension arm. In that case, the wheel spindle (4) is clasped on the right or left side and the wheel hub (1) is completely closed from one side.
From the moment the steering axle (3) turns to the left or the right, the wheel hub (1) will follow and also rotate around the steering house (2). The maximum steering angle λH of the wheel hub (1) is defined by diameter and width of the wheel hub (1) and the diameter of the wheel spindle (4). The configuration of the steering house as depicted in figures 1, 2 and 4 allows for a steering angle λH of 24°.
Steering the wheel is done rotating the steering axle (3) by means of electrically or hydraulically driven actuators inside the steering house (2).
If hydraulic power is used the steering can be achieved by opting for a rotary actuator or a piston actuator.
-
Rotary actuator (figures 2 and 3): The steering axle (3) is connected to the rotor (10) that divides the space within the steering house (2) in multiple separated chambers (X, Y, U, V). The more chambers, the more restricted the steering angle λH becomes. All chambers are filled with hydraulic fluid under pre-pressure. As soon as the pressure is increased through the hydraulic line (11), the pressure in chamber U and V rises. The rotor (10) will move clockwise and the hydraulic fluid in chambers X and Y is pushed away via the hydraulic line (12). If the pressure is increased through the hydraulic line (12), the pressure in chambers X and Y rises, the rotor (10) rotates counter clockwise and the hydraulic fluid in chambers U and V is pushed away through the hydraulic line (11). The larger the dimensions, diameter and height, of the steering house (2) and the larger the number of rooms, the lower the pressure built-up in the rotary actuator. For the steering of a motorcycle the steering house configuration, as depicted in figures 2 and 3, necessitates a maximal pressure of 12 bar on top of the pre-pressure.
​
Click here to look at drawings of CSS Rotorsteering
Click here to look at movies of CSS Rotorsteering
​
-
Piston actuator (figures 4 and 5): The piston actuator uses the available space inside the steering house (2) and the wheel spindle (4). The piston-rod (15) has pistons (16) at both ends and can move in both directions within the wheel spindle (4). The chambers R and S are filled with a hydraulic fluid. When the pressure in chamber R increases by supply of hydraulic fluid through the hydraulic line (13), the piston-rod (15) will move to the right. The hydraulic fluid in chamber S is drained away through the hydraulic line (14). The gear plate (17) turns the axial movement of the piston-rod (15) into a rotating movement of the steering axle (3). When the piston-rod (15) moves to the right this results in a counter clockwise rotation of the steering axle (3). Conversely, when the pressure in chamber S increases through supply of hydraulic fluid through the hydraulic line (14), the piston-rod (15) will move to the left and this will result in a clockwise rotation of the steering axle (3). The gear plate (17) is journalled (D) in the steering house (2). By doing so the gear plate (17) can be manufactured broader than the piston-rod thereby creating extra space for the steering axle (3) with the gear wheel which results in a longer lever arm. The longer the lever arm, the lower the necessary steering pressure. The gear plate (17), journalled in the steering house (2), ensures the piston-rod (15) only being stressed in axial direction, enabling optimal and precise steering. The larger the diameter of the wheel spindle (4) and the steering house (2), the lower the steering pressure in the chambers R and S. For the steering of a motorcycle, the steering house configuration as depicted in figures 4 and 5 needs a maximal pressure of 40 bar. When increasing the diameter of the wheel spindle (4) to 70 mm, the maximal pressure drops to 17 bar. As stated above, the diameter of the wheel spindle (4) has a significant impact on the steering angle λH. For a steering angle λH of 24°, the diameter of the wheel hub (1) will increase by 20 mm with an increase of the diameter of the wheel spindle (4) to 70 mm.
​
Click here to look at drawings of CSS Pistonsteering
Click here to look at movies of CSS Pistonsteering
The rotary actuator (figures 2 and 3) or the piston actuator (figures 4 and 5) spins the steering axle (3). Likewise, the wheel hub (1) connected to the steering axle (3) rotates around the steering house (2). There is no mechanical connection between the steer (18) and the wheel hub (1).
The steering: how does it works?
​
In case steering is done hydraulically, the hydraulic pressure that steers the rotary actuator or piston actuator in the steering house (2) is transferred by hydraulic fluid through the hydraulic lines. This pressure can be generated by a power steering device (motor-driven hydraulic pump). To this end, recourse can be made to long known and tested steering systems from the automobile world and the industry. Such systems take up space, are not cheap and weigh a couple of kilograms. Since no mechanical connection exists between the steer (18) and the wheel hub (1), this power steering will preferably be electrical to allow steering with a non-running engine using the power from the battery.
For lighter and/ or sportier vehicles where cost and weight play an important role and / or in case no power supply for power steering can be called upon, a hydraulic system without power steering is a preferred option.
The CSS can make use of a light and compact hydraulic system without power steering.
A description of this hydraulic steering system without power steering is given. For the sake of simplicity the reservoir for the hydraulic fluid and the temperature compensator, needed for a stable pre-pressure and the absorption of the variations in the volume of the hydraulic fluid due to increasing and decreasing temperatures, are left out.
​
-
The steering movement is directly and under all circumstances transferred from the steer to the wheel hub (1). In order to do so a second rotary actuator (19) or a second piston actuator (20), depending on the chosen option, is situated under the steer. The steer (18) is fitted to the steering axle (21) of these actuators.
-
Rotary actuator: If the steer (18) turn clockwise, hydraulic fluid is transferred from the chambers X and Y of the rotary actuator (19) that is connected to the steer, via the hydraulic line (11) to the chambers U and V of the rotary actuator (23) in the steering house (2). This causes the steering axle (3), together with the wheel hub (1) and the wheel to turn clockwise.
-
Piston actuator: If the steer (18) turns clockwise, hydraulic fluid is transferred from the chamber R of the piston actuator (20) that is connected to the steer, via the hydraulic line (14) to the chamber S of the piston actuator (24). The steering axle (3) makes the wheel hub (1) and the wheel turn clockwise.
The monitor and compensation device
​
In case the hydraulic components are designed sufficiently accurately and taking the relatively low hydraulic pressure that occurs in the hydraulic system into account, the possible deviation between the steering angle of the wheel hub (1) λH and steer (18) λS will be very small. Nevertheless, a deviation needs to be considered and therefore it has to be possible to monitor and adjust for the deviation under all circumstances, thereby guaranteeing a safe and optimal steering feel.
​
In order to maintain the steering angle of the wheel hub (1) λH and the steer (18) λS perfectly synchronously the CSS is equipped with a monitor and compensation device. For this purpose both the steering angle of the wheel hub (1) λH and the steering angle of the steer (18) λS are measured by an angle sensor and the data are permanently transferred to the ECU (22).
​
The ECU (22) will monitor the λH – λS deviation and apply corrections, taking the direction and the speed of the wheel hub (1) λ'H and steer (18) λ’S into account. Furthermore, the ECU (22) can also use additional data originating from other sensors, if present, such as speed, acceleration, braking force, position of the throttle, lean angle and other.
​
The ECU (22) shall use the received information and input from the angle sensors and maintain the steering angle of the wheel hub (1) λH and the steer (18) λS perfectly synchronously using the following rules:
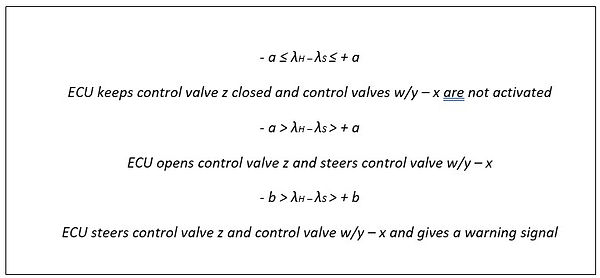
The angular deviation tolerances a and b (a > b) are determined by the constructor or can be chosen by the user within the range of certain minimum and maximum values.
​
There are two possible systems: one without steering damping (figure 6) and one with steering damping (figure 7).
-
ECU + control valve z (figure 6): The ECU (22) will steer the control valve z and by doing so limit the deviation between both angles λH and λS within the values a and b chosen by the constructor, considering the steering angle of the wheel hub (1) λH and the steering angle of the steer (18) λS , the deviation λH – λS , the direction and the speed of the wheel hub (1) λ'H and steer (18) λ’S.
-
ECU + control valves z - w/y – x (figure 7): The CSS device can easily be combined with an additional rotary actuator (25) or and additional piston actuator (26) performing also as steering damping. Such an electronic steering damper by means of a rotary actuator is already applied by Honda (cf. Honda HESD European patent 0 4012506.4 publication 18.08.2011 Bulletin 2011/32). The ECU (22) can switch on this additional hydraulic actuator in the compensation process in order to maintain the steering angle of the wheel hub (1) λH and the steer (18) λS perfectly synchronously. The use of the additional w/y – x control valve ensures an even more precise regulation and control. The ECU (22) will steer the control valves z and the w/y – x and by doing so limit the deviation between both angles λH and λS within the values a and b chosen by the constructor, considering the steering angle of the wheel hub (1) λH and the steering angle of the steer (18) λS , the deviation λH – λS , the direction and the speed of the wheel hub (1) λ'H and steer (18) λ’S.
If the angular deviation λH – λS exceeds the maximum angular deviation tolerance b, the monitor and compensation device does not function properly. The user will be informed by a visual or auditory warning signal. The user will stop the vehicle and can manually steer the control valve z and align the steer (18) and the wheel hub (1) by pressing the reset button of the ECU (22). As soon as λH – λS = 0, the pressure control valve z is closed and the steer (18) and the wheel hub (1) are synchronized again.
​
The same procedure is followed each time the vehicle is started. When the power supply fails, the driver or operator can correct the angular deviation between the steer (18) and the wheel (6) by manually operating the control valve z and moving the steer (18) back and forward.
​
If only the control valve z is used the constructor will connect, of both used actuators - one inside the steering house (2) and one connected to the steer (18) in theory perfectly identical but in reality slightly deferring - the actuator with the largest volume yield per degree of rotation to the steer (18).
​
Based on the information coming from the angle sensors the ECU calculates the angular position of the steer λS and of the wheel hub λH, the angular deviation λH – λS, the angular velocity of the steer λ’S and of the wheel hub λ'H and the difference in angular velocity λ'H – λ’S. The ECU (22) will steer the control valve z and if a steering damper is present also the valve w/y – x, based on a decision-table taking into account the 20 possible combinations of angular position and angular velocity λ'H – λ’S. If other sensors are present this information can be taken into account by the ECU.
